Metal waste is piling up. Companies face a common problem—how to effectively reduce metal scrap. The answer? Metal shredding machines. But not understanding how they work could cost businesses money and resources. That’s a problem. If you don’t know the process, your team could be stuck in a cycle of inefficiency.
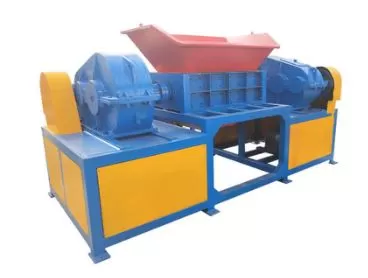
Metal shredders are powerful machines designed to break down large metal pieces into smaller, manageable parts. They work through a series of rotating blades that slice the metal into smaller fragments, making it easier to recycle and reuse.
Metal shredders are not only efficient but also a great way to save on waste management costs. Who doesn’t love saving money while protecting the environment? It’s like hitting two birds with one stone—except no birds get hurt, of course.
How does a metal shredder actually break down metal?
The key to understanding how metal shredders work is knowing their structure. Think of the machine as a well-trained wrestler, ready to tear through any metal. It’s equipped with sharp, heavy-duty blades made of hardened steel. These blades rotate at high speeds and grab onto the metal fed into the machine, tearing it apart. The rotating mechanism, combined with the machine’s sheer power, makes short work of even the toughest metals.
The blades are positioned in such a way that they “bite” into the metal, breaking it down bit by bit. This creates small, uniform pieces of shredded metal that can be easily transported, melted, or recycled.
What happens to the metal inside the shredder?
After the metal is pulled into the machine, the shredding process begins. It doesn’t just happen in one quick motion. The metal goes through multiple stages. First, it’s cut into larger chunks. Then, the smaller pieces are continuously ground down as they travel further inside the machine.
Imagine putting a large metal object into the shredder—it gets grabbed, crushed, sliced, and finally turned into smaller parts. But wait, there’s more. Magnetic separation technology is often used to pull out any non-ferrous metals like copper or aluminum, ensuring the purest output [source needed]. It’s an intricate process, but fascinating to watch.
What types of metals can shredders handle?
Not all metals are equal, and neither are metal shredders. The types of metals a machine can handle depend on its design. Heavy-duty shredders can tear through materials like steel beams, aluminum, copper, and even cars! Yes, entire cars! These machines are beasts.
On the other hand, smaller shredders handle lighter metals, like aluminum cans or metal sheets. The machine can even adjust based on what type of metal you’re dealing with—talk about smart technology.
What are the benefits of using a metal shredder?
Using a metal shredder is not just about reducing the size of scrap metal; it’s about increasing efficiency across the board. First, it saves space. You wouldn’t believe how much room unprocessed metal can take up. Shredding allows you to store and transport the metal more efficiently, reducing costs.
Next, there’s the environmental impact. Shredded metal is easier to recycle, meaning less waste ends up in landfills. Plus, shredding metal reduces the need for new raw materials. So, your company gets to cut costs and reduce its carbon footprint—a win-win situation if you ask me.
How is safety maintained during the shredding process?
Let’s face it, metal shredding is a serious business. Safety is the top priority. Modern shredders are designed with built-in safeguards to prevent accidents. These include emergency shutoff buttons, guarded feeding systems, and smart sensors that detect jams or overheating.
Operators are also trained to feed the metal into the machine at a consistent pace. Feeding too much at once? That’s a recipe for disaster. The machine will jam, and nobody wants to deal with a jammed metal shredder. Trust me, I’ve seen it happen.
What maintenance does a metal shredder require?
Like any complex machine, metal shredders need regular maintenance. The blades will wear down over time, especially when cutting through tougher metals. Replacing or sharpening the blades is a routine part of upkeep. The motors and hydraulic systems also need to be checked frequently to ensure they are operating at full capacity.
Routine maintenance isn’t just for keeping the machine running; it also extends its lifespan. And a long-lasting machine is great for your bottom line. After all, no one likes unexpected repair costs popping up.
Can metal shredders handle more than just metal?
While “metal shredders” seem pretty niche, they can actually shred more than just metal. Many shredders are designed to handle plastics, wood, and even tires. This versatility makes them an indispensable tool for many industries [source needed]. Imagine having one machine that can tackle multiple materials.
Of course, the settings and blades need to be adjusted when switching materials, but it’s nothing that a well-trained operator can’t handle.
Conclusion
Metal shredding machines are an essential part of modern waste management and recycling. They take tough materials, like steel and aluminum, and break them down into smaller, manageable pieces. With rotating blades, smart technology, and built-in safety features, these machines are the unsung heroes of recycling and manufacturing.
Understanding how they work not only helps you appreciate the technology but also allows you to make smarter, more efficient business decisions. So, whether you’re dealing with metal scraps, reducing waste, or just looking for a way to cut costs, metal shredders are the way to go.